La semaine dernière, je vous présentais la dernière création automobile de Gordon Murray, la citadine T25. Mais l’ingénieur ne s’est pas contenté de concevoir une auto révolutionnaire. Il a également totalement repensé le procédé de fabrication d’une voiture. Un procédé à l’image de la T25 : léger, flexible, écologique et économique. Murray l’a baptisé iStream, et compte bien le commercialiser à de grands groupes… automobiles ou non. La révolution est en marche !
Depuis que l’automobile est produite en grande série – c’est à dire depuis la Ford T… en 1913 ! – aucune innovation fondamentale n’a bouleversé le processus de fabrication. Si les robots ont débarqué en masse, le cœur de métier consiste toujours à assembler des éléments de carrosserie et de structure en acier, éléments eux-mêmes formés à l’aide de presses hydrauliques. Une industrie lourde, bruyante, dévoreuse d’énergie et d’espace.
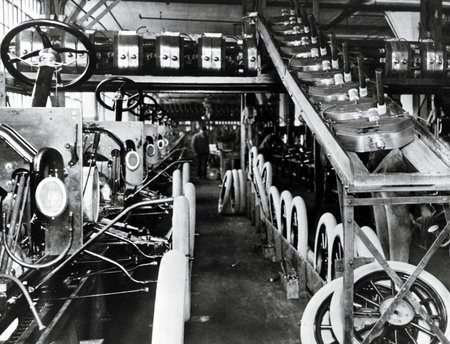
L’usine Ford de Highland Park (1913). Aujourd’hui il y a des robots en plus, mais sinon rien n’a changé !
Mais, justement, la T25 n’est pas dotée d’une coque en acier, mais d’un simple châssis tubulaire revêtu d’une carrosserie en plastique recyclé. Du coup, pas besoin de presses hydrauliques. En outre, la voiture est compacte et compte 20 % de pièces de moins qu’une citadine de conception ordinaire. Résultat, une usine fabriquant la T25 sera cinq fois plus petite qu’une usine automobile classique à production égale, et consommera également 5 fois moins de ressources énergétiques. Par conséquent, la mise de fonds initiale est également réduite.
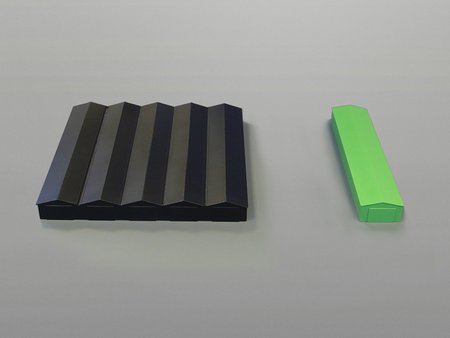
Pas de bruit, moins d’espace, moins de consommation énergétique : une usine iStream peut être implantée n’importe où
La production de l’auto est plus simple, mais son transport également : la voiture peut être livrée dans des caisses plates, un peu comme un meuble en kit. Il est ainsi possible de faire tenir douze fois plus de caisses en blanc dans un container standard, ce qui réduit d’autant les émissions de CO2 et les coûts de transport. Mieux : l’usine de production étant compacte et silencieuse, il est carrément possible de supprimer les contraintes de transport, en installant la chaîne de fabrication… dans l’arrière-cour d’une concession !
Mais ce n’est pas tout : Gordon Murray et son staff ont étudié 18 mois durant le cycle complet de vie de la T25, de la production des matières premières à son recyclage. On l’a vu, la carrosserie est réalisée en plastique recyclé, qui peut être à nouveau recyclé. « Mais le recyclage idéal », rappelle Murray, « c’est de ne pas recycler ! ». La structure modulaire de la T25 fait qu’il est possible de la recarrosser après une dizaine d’années, en réutilisant le châssis tubulaire. C’est autant de coûts et de pollution en moins !
« C’est la technologie de la Formule 1, mais ramenée à quelques queues de cerises ! », explique Murray, qui ajoute qu’une T25 de milieu de gamme pourrait être vendue 6 500 livres (environ 8 300 €). Le procédé iStream est par ailleurs très flexible : il s’applique pour la T25, mais Gordon Murray travaille déjà sur un projet de berline classique. Il serait même envisageable de fabriquer des minibus avec ce processus.
Pour autant, l’iStream n’est pas l’avenir de toute la production automobile. De l’aveu même de Murray, ce processus est particulièrement adapté pour des petites ou moyennes séries, de 20 000 à 200 000 voitures par an. Au-delà, la démultiplication de l’investissement dans l’outil de production ne le rend pas compétitif face à la construction classique. Ouf, les grands groupes automobiles ont eu chaud !
PS : Merci pour votre fidélité 🙂 Je pars très bientôt en vacances, et serai de retour aux commandes de ce blog vers la mi-août. Bel été à tous !
il réinvente la méhari en qq sorte!
bonnes vacances,
n’oubliez pas de rentrer tout de même …
Cela ressemble etrangememt au procede de MDI!
Je previens cette societe car son savoir faire est brevete
genial pour la ville ,vive la debrouille
en esperant que le projet arrive o bout pour une fois
cordialement .